Predictive ML models for manufacturing: Use cases, benefits, development and implementation
In the dynamic landscape of manufacturing, the transformative potential of predictive machine learning models is becoming increasingly evident. These models serve as instrumental tools, strategically guiding the industry toward optimization, elevated product quality, and reduced downtime. The Manufacturing Leadership Council Report states that 43% of manufacturing players strongly agree with the AI advantage in predictive maintenance, and an additional 48% moderately agree. Furthermore, investment of AI for manufacturing is in an upward direction, with 96% of companies expected to boost their investment levels by 2030. This underscores the growing recognition of the pivotal role that artificial intelligence plays in reshaping the manufacturing landscape. Contact Us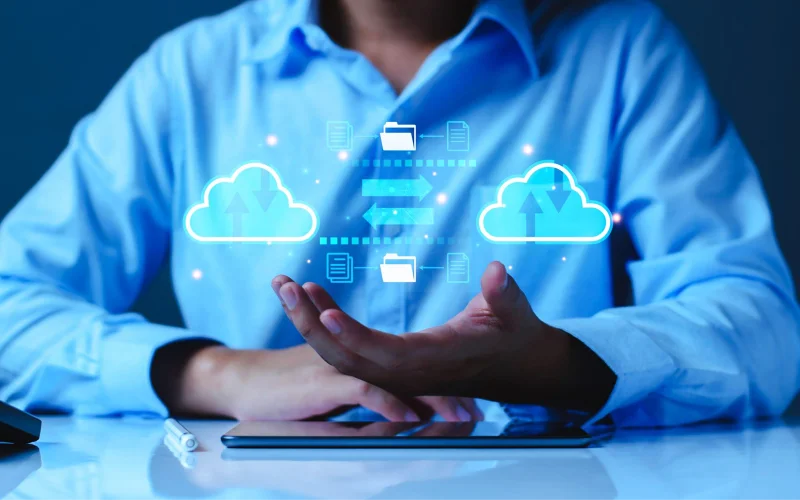
In the context of Industry 4.0, transformative technologies span four interconnected verticals: connectivity and data optimization, analytics with intelligence, human–machine interactions, and sustainable manufacturing processes. From cloud computing to additive manufacturing, these verticals collectively propel Industry 4.0, reshaping production’s future through improved communication, data accessibility, operational efficiency, and sustainable solutions. The digitization of factories, supply chains, and production processes presents both unprecedented opportunities and challenges.
As we understand the foundational pillars of Industry 4.0, now, let’s delve into the transformative role of artificial intelligence within the manufacturing sector. AI models are pivotal in transforming manufacturing processes. Manufacturers extract valuable insights from extensive datasets generated throughout the production process by leveraging machine learning algorithms and advanced analytics. Predictive models empower proactive decision-making, forecasting equipment failures, optimizing maintenance schedules, and preventing costly downtimes. Moreover, AI enhances quality control by identifying real-time patterns and anomalies, ensuring a consistent and high-quality output.
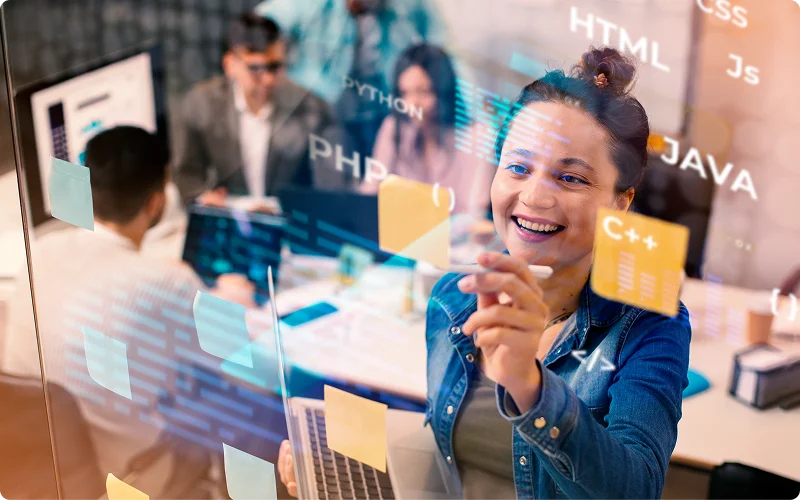
How can predictive machine learning models help manufacturing operations?
In today’s modern manufacturing landscape, predictive machine learning models have emerged as powerful tools that transform decision-making, optimize processes, and drive efficiency.
For example, by analyzing historical data from sensors, equipment logs, and maintenance records, machine learning models predict when the machine or equipment is likely to fail. This foresight enables proactive maintenance, preventing unexpected breakdowns and reducing production downtime.
Also, manufacturers can identify and address quality issues before they escalate into more serious problems. ML models detect anomalies, deviations, or patterns indicative of potential defects by analyzing real-time data from production lines. Early detection allows corrective actions, reducing the number of defective goods produced.
Predictive models aid manufacturers in anticipating demand fluctuations. Machine learning models forecast future demand by analyzing historical sales data, seasonality, and market trends. With this knowledge, manufacturers can optimize inventory levels, production schedules, and resource allocation. Machine learning models can also predict workforce demands based on historical data, employee performance, and market dynamics. Organizations can effectively plan recruitment, training, and skill development by understanding staffing needs.
Predictive models empower manufacturers to make informed decisions, enhance productivity, and stay competitive in an ever-evolving industry. As technology advances, harnessing these models’ potential will be crucial for sustainable growth and innovation.
Top use cases of predictive models in the manufacturing sector
Before diving into the implementation of AI-driven predictive maintenance across diverse sectors, it’s essential to follow a systematic approach. Here’s a step-by-step guide to guide you through the process:
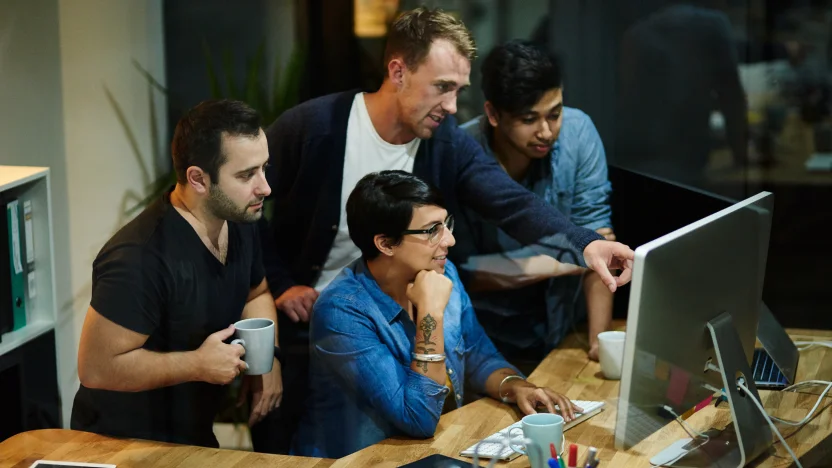
Predictive maintenance and operations
As the Wall Street Journal reported, industrial manufacturers incur an estimated $50 billion annually due to unplanned downtime, with 42% attributed to equipment failure. Such unforeseen outages lead to increased expenses for maintenance, repairs, and equipment replacement, emphasizing the critical impact of technology in mitigating these challenges. And this is where AI-powered machine learning in predictive maintenance makes its best case.
Predictive maintenance (PdM) is a primary and fundamental application of predictive machine learning models in manufacturing. Studies from the U.S. Department of Energy’s Federal Energy Management Program reveal that an effective predictive maintenance program in manufacturing yields savings of 30-40% over reactive maintenance and 8-12% over preventative maintenance, highlighting the substantial financial benefits of proactive approaches in the industry.
Quality control and defect detection
Quality control has traditionally been reactive, identifying defects after they’ve already affected production. Predictive quality control disrupts this norm. By analyzing real-time data from sensors, production logs, and quality inspections, manufacturers can anticipate and prevent quality issues before they arise. This proactive approach significantly lowers the production of defective goods, elevates product standards, and ultimately enhances consumer satisfaction and loyalty.
Whether it’s detecting faulty components on an assembly line or ensuring consistent product quality, predictive models play a pivotal role. Predictive models analyze real-time data from sensors and production logs to detect anomalies and patterns indicative of defects. Early identification allows manufacturers to take corrective actions, reduce defective goods, and maintain high-quality standards. Staying ahead of quality issues is not just good practice—it’s a strategic advantage in today’s competitive market.
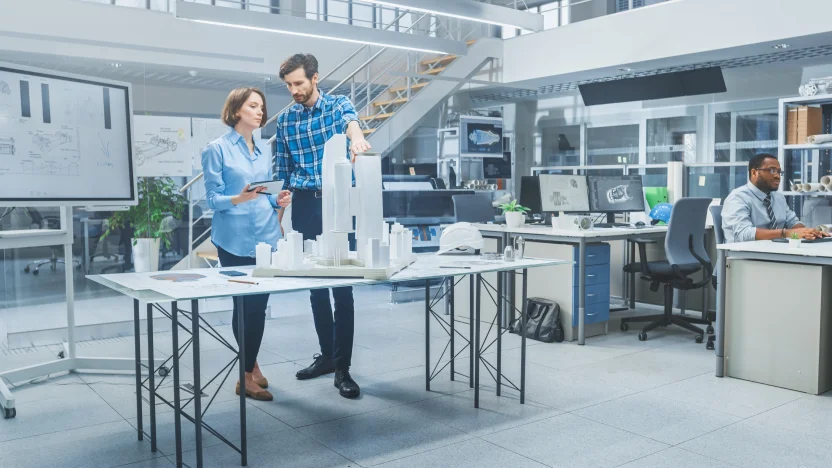
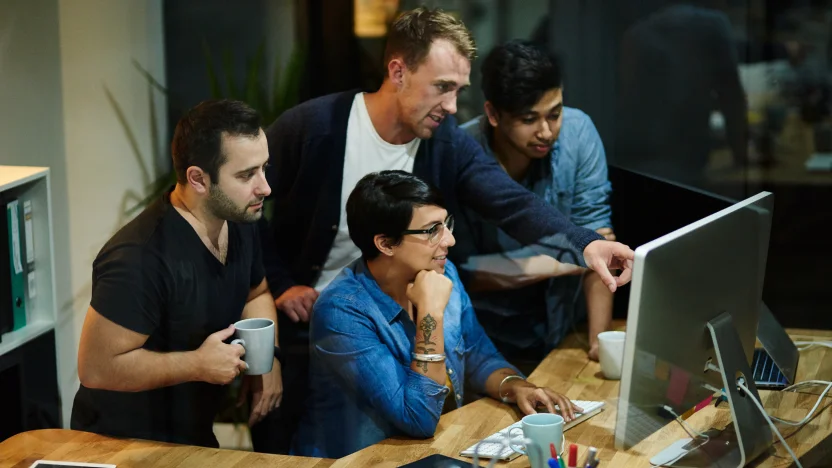
Demand forecasting
Predictive machine learning models in manufacturing help firms anticipate demand fluctuations. According to a Gartner survey, 45% of companies already use AI techniques, and 43% plan to use AI-powered demand forecasting within two years. Machine learning models forecast future demand by analyzing historical sales data, seasonality, and market trends. Manufacturers can optimize inventory levels, production schedules, and resource allocation with this knowledge. The result? Tangible cost savings and streamlined operations. Moreover, predictive models aid in inventory management—preventing stockouts, reducing excess inventory, and maintaining just-in-time supply chains.
Data-driven demand forecasting goes beyond traditional methods, incorporating various influential factors. These tools adeptly capture real-time shifts in purchase behavior, emerging social trends, weather patterns, inflation data, and supply chain information. Whether it’s sudden spikes in demand due to social media trends, unexpected shifts caused by external events, or churn predictions powered by machine learning systems, these models keep manufacturers informed about every single aspect. They can harness the power of both in-house and external data sources, employing machine learning to swiftly analyze massive datasets, ensuring timely and accurate insights into evolving demand dynamics.
Supply chain optimization
Predictive machine learning models in manufacturing optimize supply chain operations. From procurement to distribution, manufacturers can make data-driven decisions. These models consider lead times, transportation costs, supplier reliability, and demand variability. Predictive models factor in lead times—the time it takes from placing an order to receiving the goods. By using predictive models to analyze historical data and supplier performance, manufacturers can fine-tune lead times. By analyzing historical data and supplier performance, manufacturers can fine-tune lead times. This precision ensures timely production and delivery, minimizing costly delays. By minimizing supply chain disruptions, manufacturers ensure timely production and delivery. Additionally, predictive models assist in supplier selection, risk assessment, and contract negotiation.
Manufacturers benefit from its multifaceted capabilities by applying predictive models for supply chain optimization. Supplier selection becomes a strategic process driven by insights derived from historical performance data. This approach not only aids in finding reliable partners but also remarkably improves on-time delivery rates. As per the Supply Chain Brain guide, manufacturers aim to find ways to automate 60-70% of predictive and prescriptive tasks. And how to achieve this? By integrating predictive ML models.
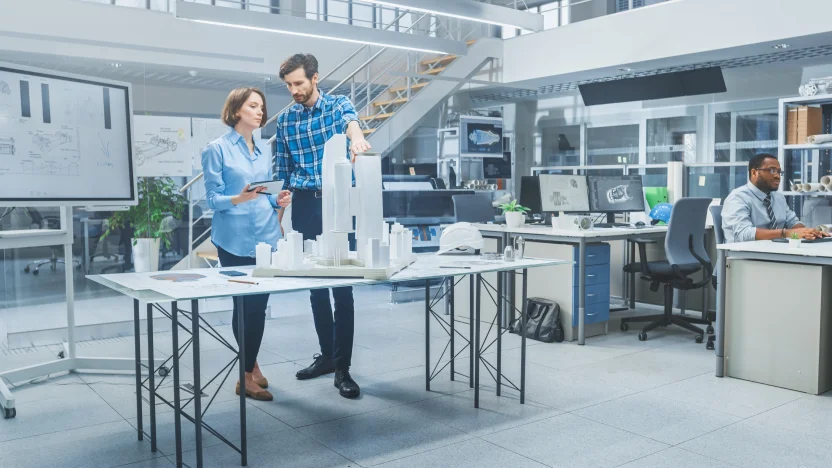
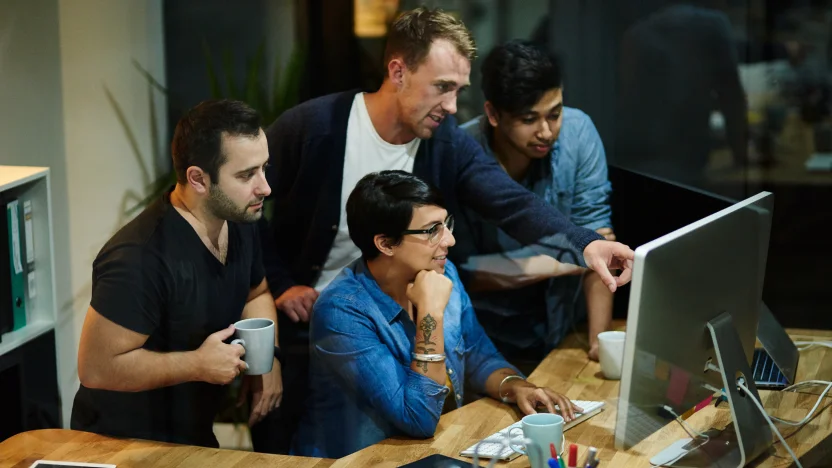
Facility optimization and process improvement
Predictive modeling aids in optimizing production processes. Predictive models help identify bottlenecks, reduce waste, and improve output by analyzing historical data. Whether fine-tuning production parameters, streamlining assembly lines, or enhancing energy efficiency, these models enhance facility performance. Furthermore, they guide process improvement initiatives like Six Sigma to achieve higher yield and lower defect rates. These points illustrate how predictive machine learning models in manufacturing contribute to effective facility management and operational excellence:- Identifying bottlenecks and waste reduction: Predictive models scrutinize historical data from production lines, enabling the pinpointing of bottlenecks. Addressing these constraints can lead to a significant increase in production throughput.
- Fine-tuning production parameters: Predictive models aid in the optimization of critical production parameters such as temperature, pressure, and speed. The fine-tuning of these settings results in consistent quality output and reduced variability.
- Streamlining assembly lines: Predictive models assess assembly line performance, facilitating the streamlining of workflows, minimizing idle time, and optimizing task allocation. These optimizations collectively contribute to a substantial reduction in production cycle time.
Workforce safety and productivity
Predictive models can assess workplace safety risks. By analyzing incident data, environmental factors, and employee behavior, manufacturers can proactively address safety concerns. Predictive models help identify potential hazards, recommend safety protocols, and prevent accidents.
Moreover, several manufacturing companies are using wearable technologies to improve worker safety by collecting data on breathing, heart rate, movement, and posture. This helps managers with a real-time snapshot of workers’ well-being through a comprehensive dashboard. Additionally, sensors aid in evaluating machine compliance, detecting safety anomalies, and identifying causes of machine stoppages. This technology enables companies to assess real-time conditions on the shop floor, detect machine misuse, identify safety hazards, and reduce safety-related stoppages.
Workforce optimization ensures strategic staffing, efficient shift planning, and skill development. A safe and well-trained workforce directly impacts productivity and operational continuity. The multifaceted impact of predictive models in this domain is evident through various facets:
Assessing workplace safety risks
Predictive models can analyze historical incident data, near-miss reports, and safety-related variables. By discerning patterns and correlations, manufacturers gain the ability to address safety concerns, ensuring a secure working environment proactively.
Predicting potential hazards
These models forecast potential hazards based on real-time data, ranging from equipment failures to chemical spills or unsafe work conditions. Early hazard prediction becomes a key element in preventing severe incidents, contributing to a safer workplace.
Recommending safety protocols
Leveraging predictive insights, manufacturers can recommend tailored safety protocols to employees. These protocols encompass proper handling procedures, guidelines on personal protective equipment (PPE) usage, and emergency response strategies, fostering a safety culture.
Workforce optimization
Predictive models guide strategic staffing decisions by analyzing historical production data, seasonal trends, and demand fluctuations. Well-optimized staffing not only enhances labor utilization but also contributes to improved overall productivity.
Efficient shift planning
Considering factors like employee availability, skill sets, and fatigue levels, predictive models facilitate efficient shift planning. This ensures that the right personnel are assigned to critical tasks, reducing overtime costs.
Skill development and training
Predictive models identify skill gaps and training needs within the workforce. Manufacturers can invest in targeted training programs to enhance employee capabilities, ultimately increasing overall productivity.
Impact on operational continuity
A safe and well-trained workforce directly influences operational continuity by minimizing accidents, absenteeism, and turnover. The result is an environment that ensures uninterrupted production, contributing to an impressive on-time delivery rate.
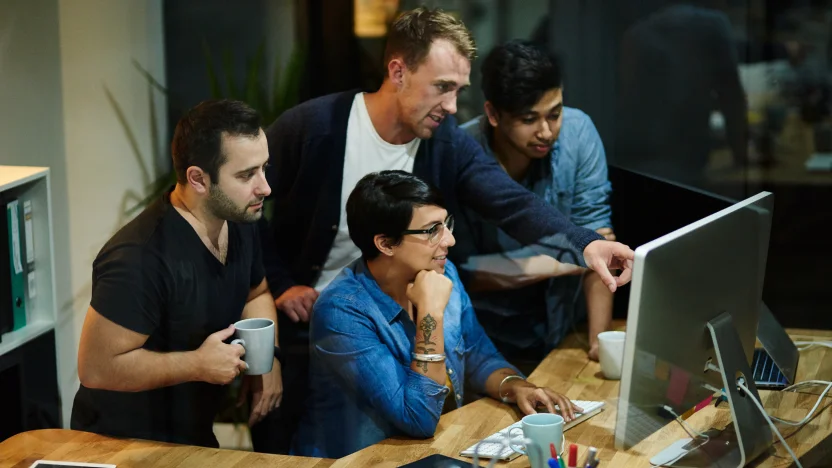
Human resources planning and talent management
Human resources planning and talent management are crucial for any organization, especially in manufacturing. Predictive models are powerful tools that can help manufacturers forecast workforce demands based on historical data, employee performance, and market dynamics.
For example, predictive models can analyze seasonal fluctuations, product demand, customer feedback, and employee turnover to estimate the optimal number and type of workers needed at any given time. Manufacturers can gain insights into their staffing needs using predictive models, enabling effective recruitment, training, and skill development. This can help them avoid overstaffing or understaffing, reduce costs, and improve productivity and quality.
Predictive models also empower strategic workforce management by facilitating talent retention, succession planning, and career development. For instance, predictive models can identify high-potential employees, assess their skills and competencies, and recommend personalized learning paths and career opportunities. This can help them retain and motivate their talent, as well as prepare them for future leadership roles.
Market analysis and strategic decision-making
Market analysis and strategic decision-making are essential for any business, including the manufacturing sector. Predictive models are a powerful tool that can provide market insights and help manufacturers make better decisions.
By analyzing customer behavior, market trends, and competitive dynamics, predictive models can help manufacturers refine their marketing strategies, launch targeted campaigns, and stay ahead of the competition. For example, predictive models can help manufacturers segment their customers based on their preferences, needs, and behaviors and tailor their products, prices, and promotions accordingly. Moreover, manufacturers can monitor and anticipate market changes, such as demand fluctuations, customer feedback, and competitor actions, and adjust their strategies accordingly.
Predictive insights can also help manufacturers launch new products by helping them test and validate their ideas, assess their market potential, and optimize their design and features. For example, predictive models can help manufacturers simulate different scenarios, such as customer reactions, price sensitivity, and profitability, and choose the best option for their product launch.
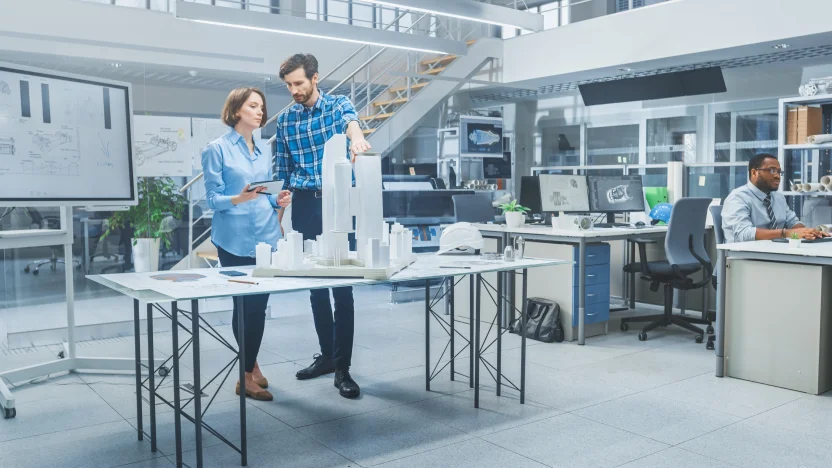
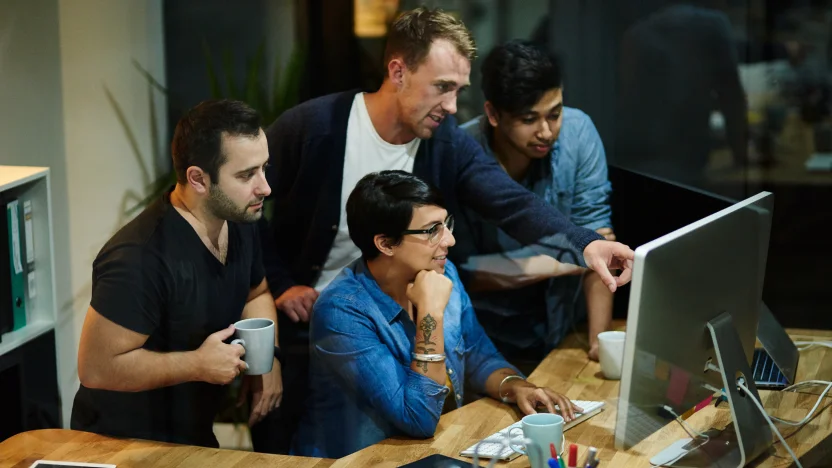
Predicting Remaining Useful Life (RUL)
Predicting remaining useful life (RUL) is a vital application of predictive modeling in manufacturing. Models forecast the remaining lifespan of machinery and equipment based on various factors, such as wear and tear, usage patterns, and maintenance history. Based on insights provided by AI models, manufacturers can optimize their replacement schedules and reduce downtime, improving their operational efficiency and profitability. Predictive RUL models are especially crucial for critical assets, such as turbines, pumps, and industrial robots, whose failure can have severe consequences, such as safety hazards, production losses, or customer dissatisfaction. Manufacturers who embrace these models stand to gain a significant edge in an increasingly data-driven world.How to build a predictive ML model for manufacturing operations?
Define the problem and objectives
As discussed in the previous section, predictive models can be applied across diverse use cases in manufacturing operations. The first step for manufacturers is to define the problem clearly and the objective of the predictive model. Some of the crucial considerations are:
- Clearly articulate the problem to be addressed by the predictive model.
- Define the objectives, including the target variable, forecasting horizon, level of aggregation (e.g., product, category, region), and evaluation metrics (e.g., mean absolute error, root mean square error).
Identify relevant data sources
The second step is to collect and prepare the data for the predictive model. This step aims to ensure data availability and accessibility for effective model training. This involves identifying and gathering the relevant data sources. The data should be cleaned, transformed, and integrated to ensure quality and consistency. The data should also be split into training, validation, and test sets for model development and evaluation.
Identify relevant data sources
The generated vectors are stored in a vector database, allowing for efficient querying and retrieval. Examples of prominent vector databases include Pinecone, Weaviate, and PGvector.
- Identify relevant data sources
- Historical sales data
- Inventory levels data
- Pricing data
- Product features data
- Customer Segments
- Operations data
- External data
- After data collection, the next step is to clean, transform, and integrate the data for quality and consistency. Some crucial steps include:
- Cleaning data: Clean the data by addressing missing values, outliers, and inconsistencies.
- Handle missing values: Remove or impute missing data.
- Remove duplicates: Eliminate duplicate records to maintain data integrity.
- Transforming data
- Feature engineering: Create new features to understand data in a better way.
- Normalization and scaling: Scale numerical features, ensuring consistent influence.
- Integrating data: Transform and integrate the data into a unified dataset suitable for analysis.
- Data merging: Combine data wherever needed for creating unified datasets.
- Ensuring consistency
- Standardizing units: Ensure uniform units of measurement across variables.
- Quality checks: Implement checks to rectify inconsistencies in data formats.
Explore and analyze the data
The third step is to explore and analyze the data to understand its characteristics, distribution, patterns, and correlations. This involves conducting Exploratory Data Analysis (EDA) using descriptive statistics, visualization, and hypothesis testing. You can uncover data patterns, distributions, and correlations through EDA, providing valuable insights to inform feature selection and model development. The exploration and analysis process is crucial for identifying the key factors that influence the objectives of the planned model. This comprehensive examination of the data sets the foundation for building an effective and accurate predictive model in the manufacturing sector.
Data splitting
The next step is to divide your dataset into training and testing subsets. The training subset is used to train your model, while the testing subset is used to evaluate its performance. The common split ratio is 75% for training and 25% for testing. You can use different libraries to achieve this.
Feature engineering
The next step is to enhance your data by extracting relevant features crucial to your predictive model’s purpose. Features are the attributes or variables that influence the outcome of your model. This step may include:
- Creating new features (e.g., ratios, aggregations).
- Normalizing or scaling numerical features.
- Aggregating historical data.
- Encoding categorical variables, for example, represent categorical variables, such as product types, in a numerical format.
- Handling time-series data (lag features, rolling averages).
Select and train the model
- Regression techniques
- Model the linear or nonlinear relationship between key manufacturing variables and outcomes.
- Examples include modeling the relationship between production efficiency and factors like raw material quality or machine settings.
- Time series techniques
- Model temporal dynamics and seasonality within manufacturing processes.
- Utilize methods like ARIMA or Holt-Winters to forecast trends and seasonal variations in production data.
- Machine learning techniques
- Capture complex and nonlinear patterns within manufacturing data.
- Apply techniques such as random forest or gradient boosting to identify intricate relationships between various manufacturing parameters.
Model evaluation and testing
Evaluate and test the model on the test set to measure how well it performs:
- Test the model on the designated test set to measure its performance and accuracy.
- Evaluate the model using the predefined metrics, such as mean absolute error, root mean square error, mean absolute percentage error, etc., to quantify the accuracy and error of the model outcomes.
- Test the model on different scenarios and periods to assess its robustness and generalizability to different situations and conditions.
Model deployment and monitoring
Great, your model is production-ready now! The next step is to deploy and monitor the model in the production environment, where it can elevate manufacturing sector operations.
- The model should be deployed in a scalable and secure way, using tools like Docker or Kubernetes, which can handle the varying workloads and ensure the availability and reliability of the model.
- The model should also be monitored for its performance, accuracy, and reliability.
- The model should be updated and retrained as new data and feedback become available. This helps automate the model lifecycle and enable continuous improvement.
Scaling and maintenance
The final step is to scale and maintain your model as your manufacturing process evolves. Adapt your model to new data, such as new products, customers, or markets. You should also consider scalability for large-scale production lines, such as cloud computing or distributed systems.
Benefits of integrating predictive models in manufacturing operations
Predictive models bring significant advantages to the manufacturing sector, enhancing various aspects of operations. Integrating predictive modeling into manufacturing processes empowers companies to make smarter decisions, enhance product quality, and drive sustainable growth. This strategic move aligns businesses with Industry 4.0 standards, providing a competitive advantage in today’s evolving manufacturing landscape. Here are the key benefits:
Optimized production planning
Predictive models analyze historical data to forecast demand accurately. This helps manufacturers plan their production schedules efficiently, preventing overproduction or stock shortages.
Improved inventory management
Predictive models enable better inventory management by anticipating demand fluctuations. They also empower manufacturers with precise churn predictions enabled by predictive capabilities. Manufacturers can maintain optimal stock levels, reducing carrying costs while ensuring products are readily available.
Enhanced supply chain efficiency
Anticipating demand allows manufacturers to streamline their supply chains. They can optimize logistics, reduce lead times, and enhance overall supply chain efficiency, leading to cost savings and improved responsiveness.
Reduced downtime
Predictive maintenance models analyze equipment data to predict when machinery will fail. This proactive approach minimizes unplanned downtime, optimizes maintenance schedules, and reduces overall maintenance costs.
Enhanced quality control
Predictive models play a crucial role in quality control by identifying patterns and anomalies in real time. This ensures early detection of potential defects, reducing the production of defective goods, elevating product standards, and enhancing customer satisfaction.
Strategic decision-making
Access to accurate predictions empowers manufacturers to make informed, data-driven decisions. Whether it’s adjusting production volumes, optimizing resource allocation, or responding to market trends, predictive models provide valuable insights.
Innovation acceleration
In manufacturing, predictive modeling catalyzes innovation. It enables manufacturers to uncover hidden patterns, identify opportunities, and foster continuous improvement. This data-driven innovation process empowers adaptive decision-making based on real-time insights, allowing manufacturers to stay ahead in a competitive market. Overall, predictive modeling accelerates innovation, enhancing the competitiveness and growth of manufacturing enterprises.
Cost savings and efficiency gains
By preventing overproduction, minimizing downtime, and optimizing resources, predictive models contribute to significant cost savings and efficiency gains. Manufacturers can allocate resources more effectively and operate with leaner processes.
Workforce optimization
Workforce optimization is a critical aspect of manufacturing processes achieved through predictive modeling. By utilizing predictive models, manufacturers can anticipate workforce skill requirements, enabling effective planning for training and recruitment. This proactive approach ensures the workforce has the necessary skills, contributing to enhanced efficiency and productivity.
Scaling and maintenance
The final step is to scale and maintain your model as your manufacturing process evolves. Adapt your model to new data, such as new products, customers, or markets. You should also consider scalability for large-scale production lines, such as cloud computing or distributed systems.
Competitive advantage
Embracing predictive modeling aligns manufacturing processes with Industry 4.0 standards, providing a competitive edge. Companies that leverage these technologies are better positioned to adapt to market changes, innovate, and stay ahead of the competition.
Challenges in building predictive models for manufacturing
Data quality and integration
Ensuring data quality and integrating diverse sources could be a big challenge for manufacturing players to build predictive models.
Skill gaps and steep learning curve
The workforce may lack the necessary skills. Solution? Comprehensive training programs to bridge skill gaps and increase the confidence of teams.
Complexity of models
The intricacy of developing and deploying predictive models can be challenging. Adopting a phased strategy, beginning with simpler models to deliver quick benefits, can help.
Cost of implementation
The initial expenses associated with implementing predictive models in manufacturing might seem substantial for businesses. But these initial investments keep the potential to bring long-term benefits to the table, ensuring a balance between affordability and rewards.
Why approach DeepSurge for predictive models tailored for manufacturing operations?
DeepSurge excels in developing predictive solutions for the manufacturing sector. With a proven track record in implementing AI technologies, including machine learning and natural language processing, DeepSurge is committed to optimizing manufacturing processes. Here’s how we can assist:
Expertise in predictive model development
Our team at LeewayHertz consists of AI experts specializing in machine learning, computer vision, and more. With a demonstrated history of implementing predictive models for manufacturing, our nuanced understanding of industry intricacies ensures the development of tailored and successful predictive models. This expertise positions LeewayHertz as a reliable partner, capable of delivering customized and effective predictive solutions that specifically address the unique challenges and opportunities within the manufacturing sector.
Domain-specific Model training
Our approach involves training predictive models on manufacturing datasets, utilizing relevant features and parameters that capture the nuances of demand patterns, production cycles, and other manufacturing-specific factors. We specialize in fine-tuning ML models to meet your requirements, whether you need to improve performance in specific domains, adapt to unique datasets, or enhance specific capabilities.
Adaptive Upgradation
DeepSurge emphasizes a transparent and adaptive approach, facilitating the evolution of predictive models in response to changing manufacturing dynamics. This includes periodic updates and retraining to ensure continued accuracy and relevance.
Client-centric approach in development
Leveraging a client-centric approach, LeewayHertz initiates a thorough consultation to deeply comprehend clients’ distinctive goals and requirements within the manufacturing sector. The development of predictive models is intricately tailored to align with the industry’s specific needs, ensuring that the solutions developed are relevant and highly effective. This client-centric methodology underscores LeewayHertz’s commitment to delivering customized and impactful predictive models precisely tailored to meet the demands of the manufacturing sector.
Endnote
In conclusion, integrating predictive machine learning models into manufacturing operations marks a pivotal paradigm shift, fostering unprecedented efficiency, cost-effectiveness, and innovation. Throughout this exploration, we’ve delved into the significant role of AI and predictive ML models, elucidating their transformative impact on manufacturing processes. The top use cases showcased the versatility of predictive modeling, ranging from demand forecasting to quality control, workforce optimization, and supply chain optimization.
Building a predictive machine learning model for manufacturing is a key initiative, demanding a systematic approach from defining the problem to deploying and monitoring the model. The benefits of such integration are multifaceted, encompassing accurate demand predictions, optimized resource utilization, and the ability to navigate dynamic market demands. We also discussed the challenges involved in this process and how association with DeepSurge helps overcome them.
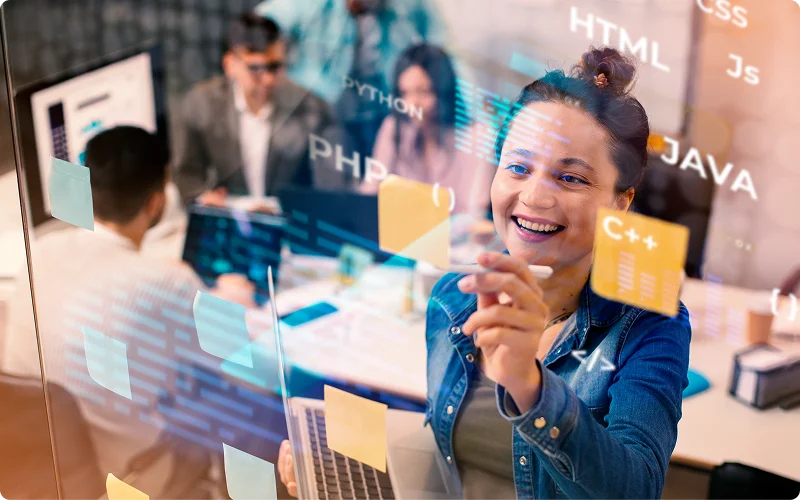
Insights
AI in inventory management: Redefining inventory control for…
AI redefines inventory management, streamlining operations, predicting demand, and optimizing stock control with unrivaled precision and efficiency.
AI in trend analysis: Predicting the pulse of…
In today’s fast-paced, data-driven world, deciphering patterns and trends is more crucial than ever, serving as a compass for organizations and individuals…
A guide to computer vision: Techniques, operational mechanics,…
Computer vision is a field of artificial intelligence that enables computers and systems to derive meaningful insights from digital images, videos, and…